|
1 前言 隨著冷鋼生產規(guī)模不斷擴大,在生產設備控制上也不斷采用新的控制理念及技術。利用變頻器傳動的交流電機所構成的調速控制系統(tǒng),以其節(jié)能,提高生產率,易于實現(xiàn)自動化控制等優(yōu)勢而在冷鋼得到廣泛使用。本文特結合煉鋼廠70t轉爐傾動裝置,對變頻調速控制系統(tǒng)簡要進行介紹。 2 轉爐傾動裝置的結構型式及特點 煉鋼廠70t轉爐傾動裝置采用全懸掛式四點傳動式,其優(yōu)點是設備布置緊湊,占地小,安裝難度較低。在實際生產操作過程中,需對轉爐傾動裝置進行頻繁的起動、制動及加減速操作,所以對傾動裝置的控制精度及系統(tǒng)的響應時間有很高的要求。 3 轉爐傾動負載特性及電動機運轉狀態(tài)分析 根據轉爐控制工藝要求,轉爐的傾動角度為正反360°,當轉爐爐口與爐底方向軸線與地平面垂直時為垂直狀態(tài),故轉爐傾動負載力矩為角度的函數,即Tfz=f(θ),屬于反阻性的位能負載。另外,根據工藝設計說明,轉爐按正力矩設計,即轉爐的耳軸下部比上部高,下部比上部重,從而保證轉爐控制系統(tǒng)的穩(wěn)定性。在轉爐傾動裝置的實際操作中,進行倒渣或出鋼時,可能出現(xiàn)負力矩。當轉爐爐體處于正力矩狀態(tài)時,電動機處于電動運行狀態(tài),當轉爐爐體處于負力矩狀態(tài)時,電動機處于發(fā)電運行狀態(tài),此時電動機處于回饋制動狀態(tài),傾動裝置的驅動電動機的機械特性和負載特性如圖1所示:
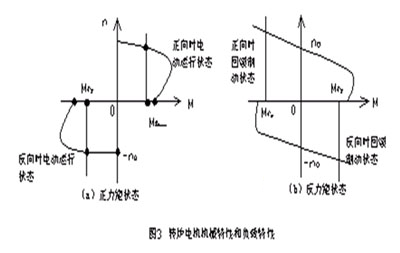
4 變頻器在轉爐傾動裝置控制系統(tǒng)的應用情況 4.1 變頻器的選擇 根據轉爐傾動裝置這種負載特性,選用變頻器的最重要的原則是變頻器必須具有在滿載或過載時輸出恒定轉矩的功能。這是因為轉爐傾動裝置具有大的慣性及四象限運行的負載特性。在實際過程中,隨轉爐傾動角度的變化及爐內所裝鋼水的流動造成其負載特性發(fā)生變化。此時電動機可能處于再生發(fā)電制動狀態(tài),所要求具有再生發(fā)電制動功能。冷鋼70t轉爐傾動裝置選用的是瑞典ABB公司生產的ACS800系列變頻器及相應的制動斬波器與制動單元系統(tǒng)。其主回路如圖2所示:

4.2 變頻器控制原理 ACS800變頻器是通過充分利用直接轉矩控制(DTC)系統(tǒng)及其主/從控制系統(tǒng)來實現(xiàn)控制功能。 4.2.1 變頻器的直接轉矩控制(DTC)系統(tǒng) 通過實時檢測磁通幅值和轉矩值,分別與磁通和轉矩給定值相比較,由磁通和轉矩調節(jié)器直接輸出所需電壓負量值。該系統(tǒng)由速度控制環(huán)和轉矩控制環(huán)組成,其中轉矩控制環(huán)是該系統(tǒng)的控制中心。并且 根據轉爐傾動負載特性的要求,具有在啟動轉爐時,必須保證變頻器在輸出的轉矩值達到負載轉矩值時,方可發(fā)出制動打開信號。 4.2.2 變頻器主/從控制系統(tǒng)。 轉爐傾動裝置為四點全懸掛式結構,它由四臺55Kw變頻電動機進行驅動。四臺電動機的輸出軸通過減速器的齒輪剛性連接相互耦合在一起,所以必須充分保證負載能夠均勻分配在四臺驅動電動機之間,使得四臺電動機的運轉速度及轉矩值基本一致。利用四臺控制變頻器所具有的主/從控制功能來保證負載可以均勻地分配在傳動單元之間。 從圖3可以看出:在四臺變頻器之間,通過光纜串行通訊鏈路組成一個環(huán)行結構網。在環(huán)行結構網中,由轉爐PLC控制系統(tǒng)對環(huán)行結構中四臺變頻器確定一臺主機及三臺從機,在主機出現(xiàn)故障時由轉爐自動控制系統(tǒng)對主機確定信號進行自動切換。轉爐自動控制系統(tǒng)所發(fā)了的轉爐傾動操作信號只與主機連接,再由主機通過光纜串行通訊鏈路來控制三臺從機。
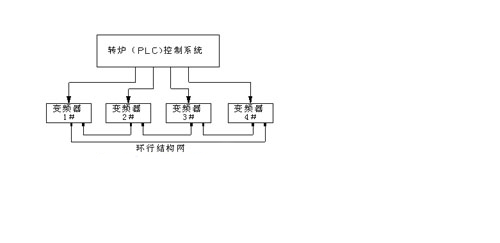
5 結語 用變頻器來控制轉爐傾動系統(tǒng),改善了轉爐起動階段時對設備的沖擊,延長了設備的使用壽命,減少了配件的更換,節(jié)約了使用成本,提高了生產效益。同時轉爐傾動系統(tǒng)屬于頻繁起動的設備,由于降低了起動電流,所以就減少了起動階段的能耗,達到了節(jié)能的效果。 由于變頻調速技術的介入,轉爐冶煉自動控制系統(tǒng)邁上了新的臺階。
|
|